
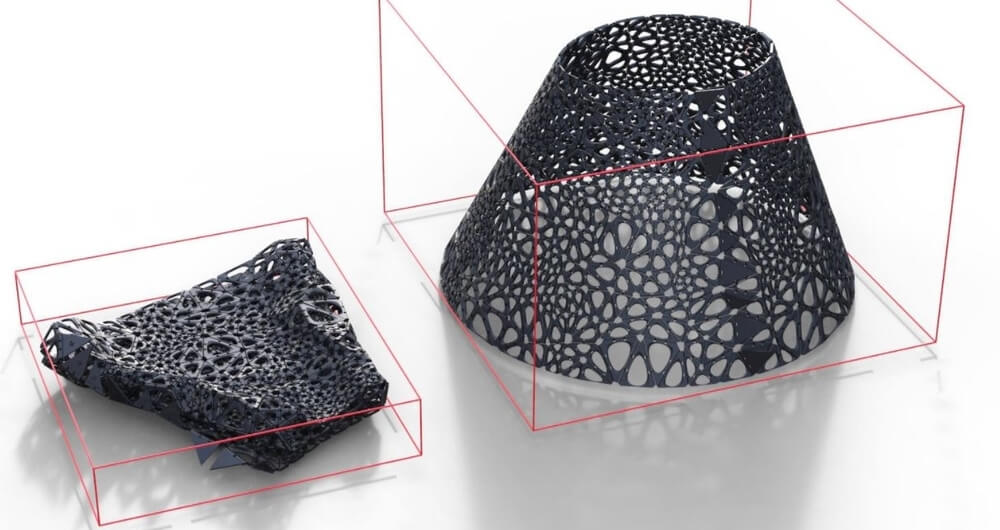
Work on the bending movement demonstrator began with designing simple, rectangular shapes with electrically conductive heating core and outer layers made with the shape memory material.įrom those simple shapes the RnD team moved to more advanced designs, eventually ending up with a bar capable of bending roughly 30 degrees within one minute from turning on the power. Under ESA contract, Zortrax had to develop three 4D printing demonstrators, each showcasing different type of electrically activated movement. This bi-material 3D printing mode was made possible by combining experimental version of Z-SUITE software, initially developed specifically for ESA, and the dual extrusion M300 Dual 3D printer which could operate with two printing heads at once. In the last step, the Zortrax RnD team checked if the two selected polymers could be printed in the bi-material 3D printing mode that enables manufacturing of parts made with two different materials. After an extensive test campaign where thermal and electrical properties of these filaments were tested, the FIBERFORCE NYLFORCE Conductive was selected as the material to heat the shape memory polymer in the 4D printed mechanisms.īending movement 4D printing technology demonstrator in the testing setup.
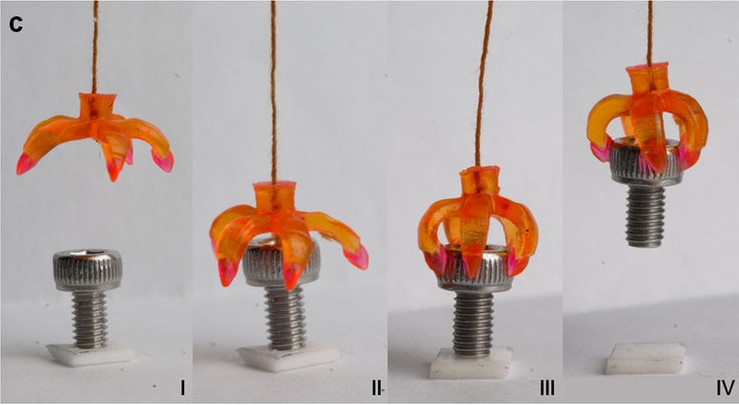
The material got delivered, thoroughly tested, and found suitable for proof-of-concept 4D printed systems.Ĭhoosing the right conductive material was easier since multiple off-the-shelf filaments met the requirements. A 4D printed mechanism with such filaments would activate on its own in temperatures exceeding 55 ℃ which happens quite often on Low Earth Orbit when the spacecraft is exposed to sunlight.įor this reason, Zortrax made a custom shape memory filament which had glass transition temperature of 75 ℃ which was 50% higher than anything available on the market. Right from the get-go, it became apparent that commercially available shape memory filaments had glass transition temperature of up to 55 ℃ which was not enough for space applications. For the RnD team selected a pool of shape memory polymers that would drive the movement in the system and a pool of electrically conductive filaments that would act as an electrically activated heater activating the shape memory effect.ĤD printing technology demonstrators delivered to ESA by Zortrax. The development process at Zortrax started with choosing the right filaments for the job. The right 3D printer which can physically make the 4D printed parts.
3d printing vs 4d printing software#
The right software which enable fabricating 4D printed parts.Right materials providing the shape memory effect.Manufacturing of 4D printed mechanisms requires three basic components. Zortrax, working with ESA, managed to solve all these problems. Because the shape changing was triggered by the environment, there was no way to deploy such structures sequentially which limited their applications.Shape changing started in relatively low temperature of 40 degrees Celsius.The process was hardly controllable – it got triggered when the environment temperature reached certain level and you can’t always control the environment.Shape changing was triggered by the environment’s temperature which heated up the entire structure at once.While their results looked impressive, there were a few apparent problems that needed solving before this technology could find any real-world applications. Now, 4D printing made headlines when the team of researchers working at MIT made deployable 4D printed structures that could move when heated to a certain temperature back in 2013. But if it was possible to get rid of the deployment mechanisms altogether, they could be made even lighter and smaller. Astronika, one of Zortrax’s key partners in space industry, can make such booms and antennas incredibly light. The weight of such structures made in a traditional way is always a sum of the structure itself and the mechanism that is supposed to deploy it.
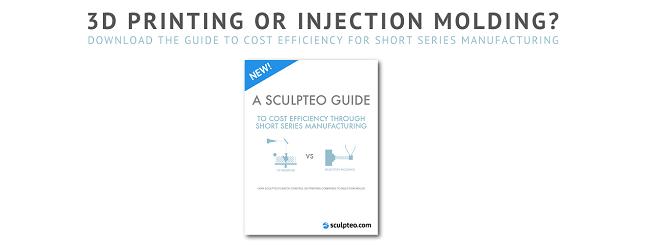
Zortrax M300 Dual 3D printer used for making 4D printed mechanisms in the ESA project.ĤD printing generated a lot of interest in the space industry because, in theory, the technology could enable engineers and mission designers to reduce weight of deployable structures like antennas, booms, or various sensors.
